Giobert SpA, a renowned OEM manufacturer of keys and locks, handles and car interiors, faced the challenge of objectifying and certifying its manual operations to ensure the highest quality for its customers and distinguish itself from competitors. In order to position itself as a manufacturer of excellence, fully in line with the dictates of lean production and industry 4.0, Giobert has adopted on a large scale an innovative digital solution for servicing manual operators: the SRv2 product from Smart Robots for error-proof manual workstations. Smart Robots has transformed Giobert’s assembly and kitting operations, delivering tangible benefits to the company, its customers, and the operators in production themselves.
Adoption of Smart Robots for packaging and assembly lines in Italy and Albania
The assembly and manual packaging of lock and starter rods are important processes for Giobert. Ensuring the highest precision and quality in these stages of production, adhering to the correct assembly sequences and avoiding errors in the kitting of components, is essential to meet the high standards of the automotive industry and to establish itself as a manufacturer of excellence.
The state-of-the-art SRv2 solution from Smart Robots, adopted by Giobert, combines innovative 3D Vision and Augmented Reality technologies to guide and support manual operators to avoid errors and improve quality and productivity.
SRv2 digitizes manual workstations, verifying operator actions in real time through vision and guiding their step-by-step activities with instructions projected on the workbench and on-screen.
The solution has been extended in lines in Italy and Albania for various assembly, kitting, machine servicing and packaging operations.
Guidance and poka-yoke control for picking, insertions, testing, and kit correctness
Specifically, the actions recognized and verified by the solution at the different locations of the lines include, among others: the common action of picking up from the supply boxes, the actual use of mechanical instruments according to defined operational sequence, the insertion of keys into the cylinder and the key-cylinder assembly into a test pad, the verification of the correct composition of the kit to be inserted into the box, recognized and distinguished thanks to the geometry of the components, and the actual packaging of the products in the appropriate containers.
Each action is verified and certified through 3D Vision, recognizing the operator’s hands and the geometry, color and height of the components.
In the event of an error, immediate feedback is returned via: i. the red light from the light turret, ii. the shapes and error indications projected in augmented reality on the bench, iii. the on-screen warnings; the operator thus can immediately notice the error, understand the action to be taken and correct himself.
At the same time, SRv2 does not send consent to subsequent machines to move forward; the system becomes completely poka-yoke, i.e., error-proof.
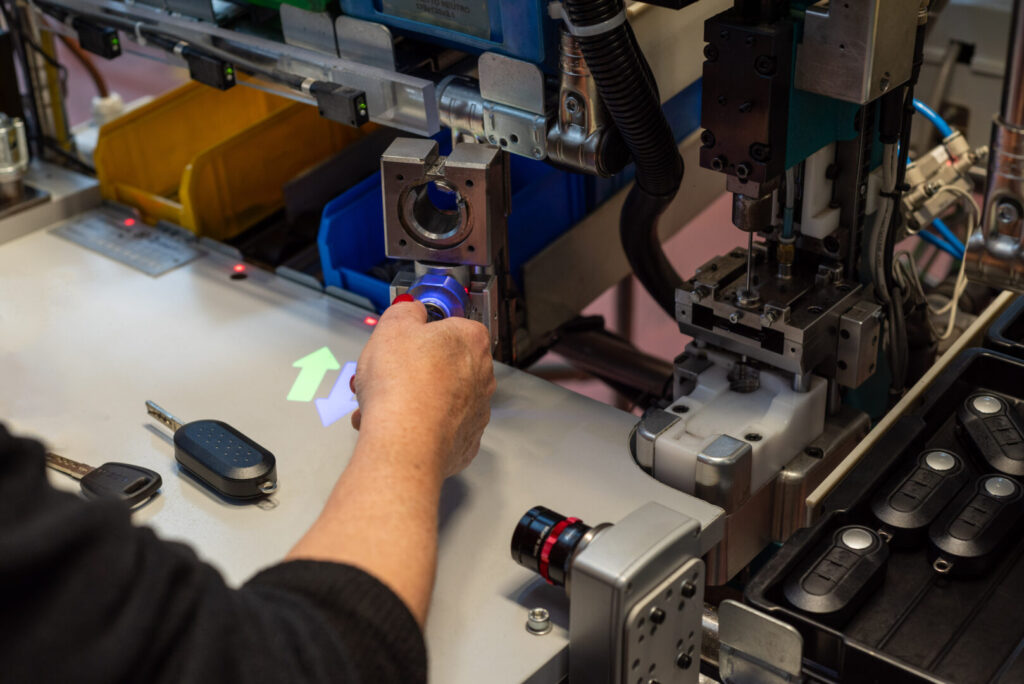
Simultaneously, SRv2 guides the operator through digital instructions projected in Augmented Reality onto the workbench and the objects themselves. Grip positions from the cassettes are illuminated, textual instructions, operational guidance images and operator aid forms such as arrows and circles are projected.
SRv2 has been fully integrated with station machines and Giobert’s production management system, streamlining operations and improving traceability and process visibility. The station machines also receive consensus from SRv2 and return their feedback, so that every signal is verified for proper process progress.
Cost reduction, customer appreciation and operator satisfaction
Through the implementation of the Smart Robots solution, Giobert has seen a tangible reduction in errors and costs associated with scrap and rework, and has received praise for the solution from its customers during their periodic audits. Digitizing the process has reduced waste, standardized the process, reduced its variability, and optimized its performance.
“Smart Robots is very supportive.
It helps me avoid mistakes and I can work without stress.”
Tiziana Palazzolo
Line operator
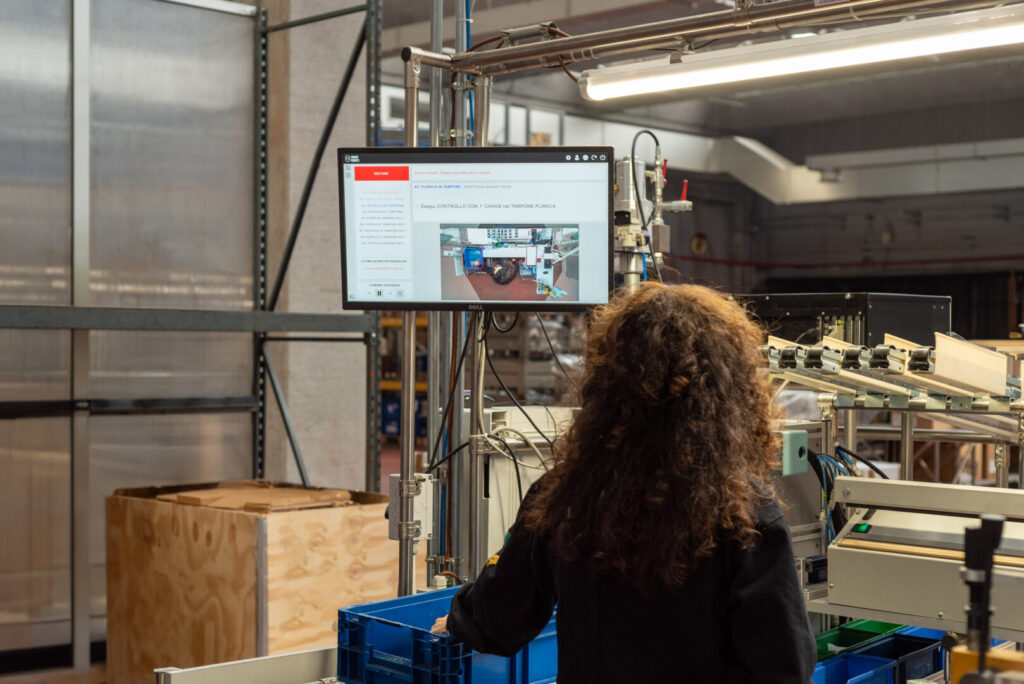
Operators have quickly embraced the new technology, appreciating its ease of use and effective support for their activities. Testimonials from Giobert employees confirm the positive impact of Smart Robots on their daily activities. Tiziana Palazzolo, a line operator at Giobert, remarked, “Smart Robots is very supportive. It helps me avoid mistakes and I can work without stress.” This positive feedback was found throughout the organization, highlighting the effectiveness and reliability of Smart Robots’ solution.
The successful case of using Smart Robots in Giobert demonstrates the transformative potential of the technology in the automotive industry, which has already been adopted by more than 50 companies in Italy and abroad to create error-proof, digital, efficient and human-centered manual workstations.