AEC Lighting is a leading company in innovative LED solutions for public, industrial and architectural lighting. AEC is distinguished by the quality of its products and its management of major international projects. The collaboration with Smart Robots supports AEC’s goal of ensuring high-quality products that are essential to their global market.
In particular, Smart Robots’ solution is used for the assembly of stadium floodlights, which are also used in the Dall’Ara stadium in Bologna and the Penzo stadium in Venice, among others.
AEC’s challenges in ensuring the quality of stadium projectors
The most important operations in the assembly of stadium projectors involve picking up the lenses, placing in the correct positions on the projector, and tightening them. Each projector includes a different number and type of lenses, from 22 to 66, to be placed in a strict pattern.
Any errors in the positioning and tightening of the lenses can result in customer complaints and returns, repair and rework costs, and, in severe cases, even the possible fall of the lens itself from the projector during assembly.
Lenses, by their nature transparent, present a challenge to conventional vision systems, which cannot use color as a distinguishing feature.
In addition, errors can also occur during the slaving of lens boxes to the workstation, associating the wrong lens models for a specific projector model.
SRv3 meets AEC’s needs through 3D vision
Smart Robots was chosen because it can guide, recognize and verify critical process operations:
- Picking the correct lens from the trays at the workstation
- Placement of the correct lenses in the correct locations on the projector
- Recognizing the lens model by measuring the different thickness (different models have differences of 4 mm in height from each other)
- Control of correct tightening sequence in poka-yoke mode thanks to the direct connection with the screwdriver
- Control of the material loading procedure to the station trays
Verify the correctness of the lenses by measuring their height: 4mm thick
Lenses are transparent, which is why traditional color- or infrared-based vision systems fail to detect their presence and correctness. Smart Robots’ 3D vision, on the other hand, also recognizes the shape of surfaces and measures the height of objects, working even with transparent objects.
SRv3 distinguishes 4, 8, and 12 mm high lenses from each other, checking whether they match the required profile for the specific projector model.
As soon as the operator inserts the lens, the system captures its 3D shape and heights and, within milliseconds, verifies whether it matches the profile of the lens chosen for that projector model at that in the specific location.
This check is crucial because different lenses must be placed in different locations in the same projector compartment, and it is important that there are no errors in positioning.
It is a recognition method that is used for objects of any shape, which is completely automatic in configuration. In fact, it is essential for clients that only a few clicks are needed to configure a new object (in this case, a new lens). In fact, only the acquisition of the image with the object and the image without the object is necessary to make it possible for the product to recognize the profile of the object.
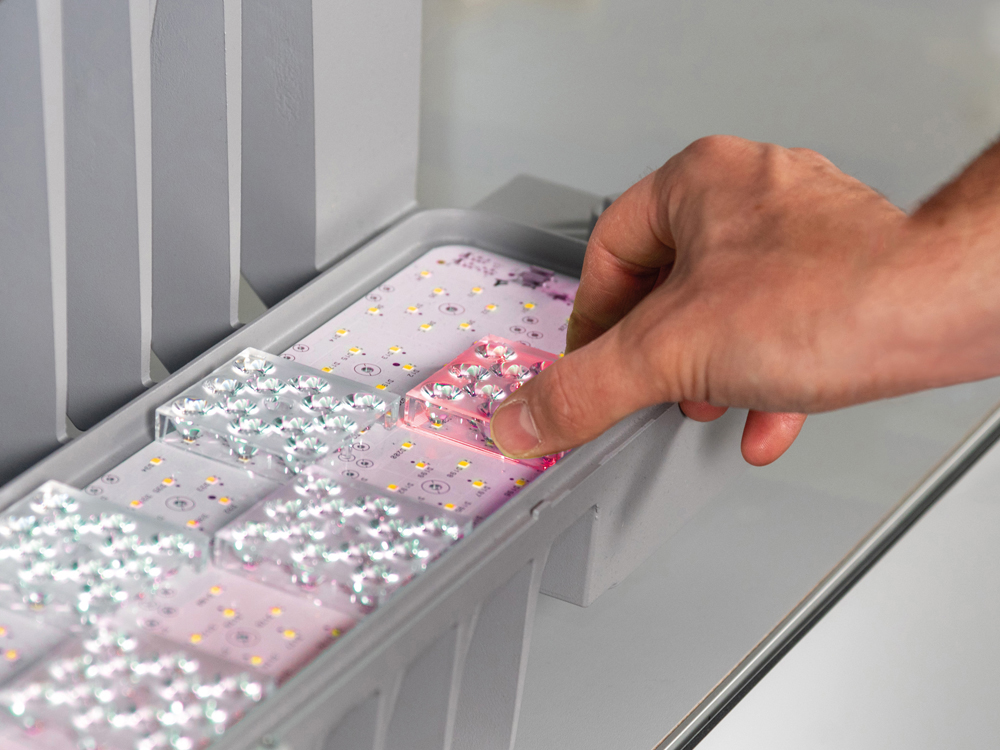
Poka-yoke control of tightening
SRv3 enables the screwdriver only in the correct positions, ensuring the exact order of the screwing sequence.
The system checks the torque signal to ensure that each screwing is completed correctly before moving on to the next.
The first phase consists of a specific sequence of tightenings in the extreme lenses in the projector, which is ensured by Smart Robots.
In the second part of the operation, the tightening of the inner lenses, the operator is free to choose the tightening sequence, and SRv3 only verifies that all lenses have been correctly screwed in.
Control of the material loading in the station trays
When the tray is empty, SRv3 verifies that the operator correctly fills the tray with the correct box lenses for the codes being assembled:
- The operator scans the barcode of the box in the shelf, which is verified by SRv3
- The operator then places the box in the correct tray and SRv3 checks its correct placement, allowing the work cycle to resume.
AEC satisfaction: better quality and faster cycle time
“Smart Robots represents a great improvement in our assembly line.
It guides the operator through each step and verifies their actions, reducing the possibility of errors and speeding up cycle time.”
Michele Fucci
Manufacturing Engineering Leader
The collaboration between AEC Lighting and Smart Robots demonstrates the effectiveness of 3D vision technology in improving the efficiency of critical assembly operations, ensuring certified quality products for the global market with relevant customer benefits:
- Quality Assurance and Cost Reduction: Elimination of positioning and screwing errors, with a significant reduction in costs associated with returns and repairs
- Competitive Advantage: AEC is distinguished by the certified quality of its products
- Operator Guidance and Job Rotation: Improved productivity and operational flexibility
- Cycle Time Acceleration: Increased production line efficiency